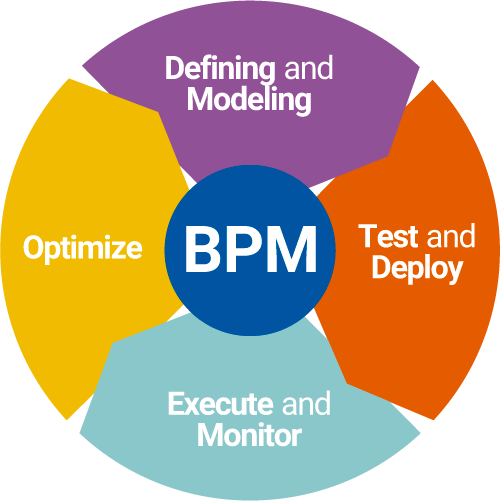
BUSINESS PROCESS MANAGEMENT
Most common mistake about BPM is considering having flowcharts of processes means BPM. BPM targets to discover, analyze, measure, improve, optimize and automate processes besides modelling them. This discpline helps organizations to standardize the way they do their businesses. This discipline is a process based discipline and processes are consist of activities. Repeatability is the main requirement of being able to name a group of business activities as Process. In this article, I aim to explain the business process management with some sample tools that you can use. To be able to do that, lets revise basic BPM targets mentioned above;
Discover: Most comman way to discover processes is using business analysts. If the company has flowcharts, analyst starts from flowcharts, checks if the flowcharts are up to date. Sadly researhes show that very few companies have their flowcharts up to date. Second step for a business analyst is trying to establish processes with the interview method with those who do the job. During discovery step every possible information about the process must be collected (Activities, Estimated Durations, Responsibles, Resources, Information to be collected during the process, Notifications etc.). With the development of technology, process mining softwares has emerged, which are tools that can partially undertake this job. If you can provide digital logs of your activities, process mining tools can turn your digital logs into processes. The use of such software will prevent you from making designs that are far from your real business processes due to incomplete information that employees will deliberately or accidentally give during business analyses.
Model: During Business Process Modeling it is recomended to use BPMN (Business Process Model and Notation). There are many advantages to use BPMN, because this notation has been designed to provide a standard readily understandable by all business stakeholders, typically including business analysts, technical developers and business managers. Another advantage of using BPMN is your designs can be easily exported or imported between different softwares if needed. This notation is improved and updated to BPMN 2.0 in January 2011. There are many BPMS (Business Process Management Software) tools in the market. Sadly Aathough they claim to be BPMS, unfortunately most of them can not offer an end-to-end solution. All of them allows you to design flowcharts and enable automation of your flowcharts but really a few of them can provide analyze, measure, and improve capabilities. And remember that having a BPMS does not mean that you are doing BPM. You should keep analyzing, measuring and improveing your processes. Integrated BPMS solutions will help you to perform these activities as an end-to-end solution.
Analyze: This analyze step mainly consists of two parts which are AS-IS and TO-BE analyses. To be able to perform an AS-IS analyze, you may use many different softwares such as BI , reporting tools even an excel spreadsheet or some BPMS includes such analyze components. The most important point in such analysis to perform them in real time. Otherwise, it may be too late to see the deviations or design mistakes in your business processes. TO-BE analysis are more like simulations for your business processes. You can simulate any possible changes in your processes and decide whether if it is going to be an improvement or not for your business. Again there are many different tools that you can perform such simulations. One of the most important point during those simulations is being able to export – import your existing business processes to your simulation tool or to be able to perform simulations in your BPMS tool. Because if you will re-design your process from scratch, as well as it will be time consuming, it will be open for making mistakes during re-designing.
Measure: For better results, you should align your strategies with your business processes. This means each process should have Performance Indicators and these indicators should be measured. These measurements will guide you how to improve your business processes. Remember that you should define accessable and strategically aligned indicators for your processes. You may use spreadsheets, or Strategy Management tools for this purpose but please keep in mind the most important point at BPM is keeping all your data up to date and traceable. Because of this reason I highly recommend you to use integrated systems. Integrate your strategy management tool with your BPMS, or prefer a BPMS which already allows you to manage your strategies.
Improve: With guidance of your measurements and process data like value added activities, non-value added activities, mandatory activities, happy paths of your processes, exception paths, costs, resource usage etc. you can improve your processes. It is very important to focus to the right process for improvement. The most common mistake made in process improvement studies is the wrong process selection. First of all, selected process to be improved has to be aligned with company strategy. Imagine that your company has both production and retail operations, and as a strategy your company aims to grow as a retailer by expending its product range. If you focus on improving production processes instead improving marketing, human resources, customer relations processes, you will not be aligned with company strategy. Regarding company strategy, management may decide to outsource production operations and if they decide to do that, improving production process may not help your company as much as you expect to be. Other important point is selecting a processes to improve by using pareto principle. Start with a valuable process for your company and try to start with small improvements which can have bigger effects. Of course while improving a process you should be careful about related process not to create bottlenecks. If any other processes as successor or predecessor may cause bottlenecks in your companies value chain you will probably not receiving expected efficiency from your process improvement. Remember that bottlenecks are not always related with duration of activities or processes, they might also be related with resources, equipment, costs, suppliers even customers of your processes. A chain is as strong as its weakest link, focus on your value chain regarding your company strategy, keep it as strong as you can and as much as you need. For instance if your company is producing super cars you do not need to improve production line automations as much as an ordinary car manufacturer.
Vedat AKSOY